先端設備と人の知恵で
徹底した品質管理を進めています。
井上ヒーターでは、弊社独自に設けた品質マニュアルに基づき、主としてフィンチューブタイプの熱交換器を製造しています。随所に最新式の設備を導入して、エンジニアたちの創意工夫も取り入れながら、常にハイレベルな生産ラインを維持しています。
現在は、ファクトリー内配置などを変更しているため、下記のファクトリー内配置図および説明は少し以前の説明です。新しい配置図と説明につきましては只今作成中につき、完成次第入れ替えいたしますのでしばらくお待ちください。
【 クリエイティブ・ファクトリー内配置図 】
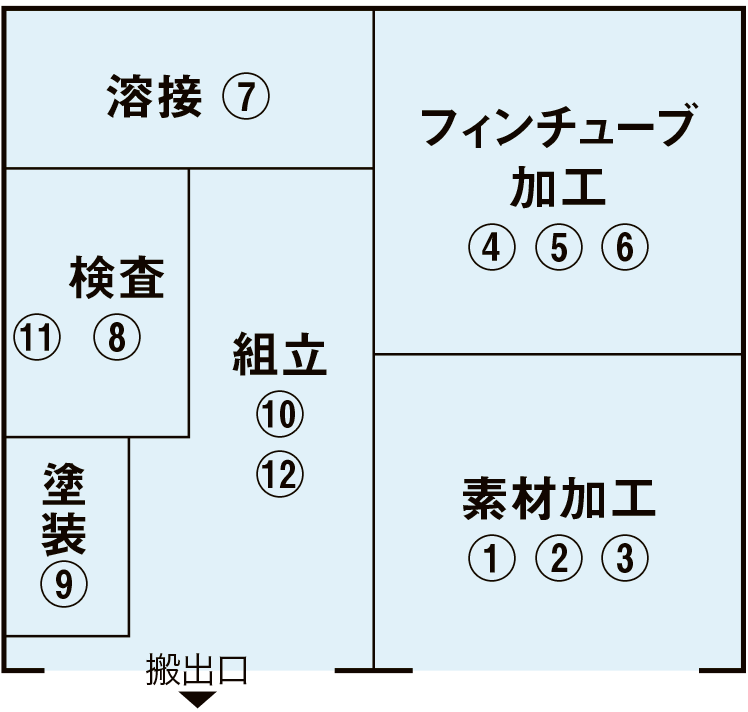
①レーザー加工機
熱交換器のケースとなる金属板を切断・加工します。レーザー加工機としては最高レベルの出力4kWを誇り、ステンレスなら12mm、鉄なら25mm厚までの切断が可能です。技術部のCADと連動しており、複雑な形状の切断、穴開け加工もスピーディーに行えます。
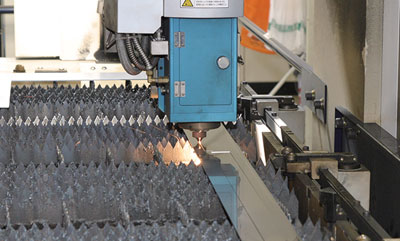
②プレスブレーキ
レーザーで切断した板金の曲げ加工を行う機械です。最大225tの圧力を掛けることができ、ステンレス板で6mm厚、長さ3mのものを箱形に折り曲げることができます。
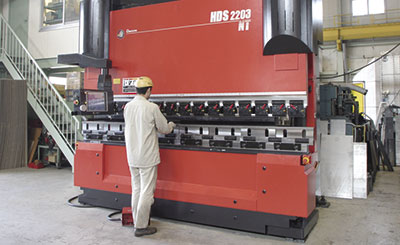
③NCドリルマシーン
熱交換器のヘッダーに取り付ける金属板の穴開け加工を行います。コンピュータにインプットした情報を読み取り、位置決め、穴開けまでを全自動で行います。
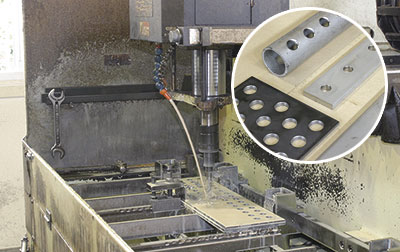
④ハイフレックスプレス(メカプレス)
コイル材料(アルミまたはステンレス)から、複雑な形状のフィン(放熱板)を高精度に整形加工を行います。熱交換器としての能力を左右する重要な工程のひとつとなります。
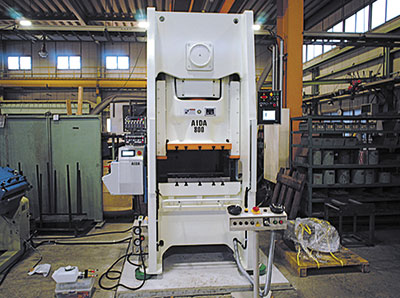
⑤全自動プレートフィン圧入機
切断したチューブにアルミまたはステンレス製のフィン(放熱板)を1枚ずつ差し込み、プレスします。完成したフィンチューブをまとめたエレメントは、溶接工程に移ります。
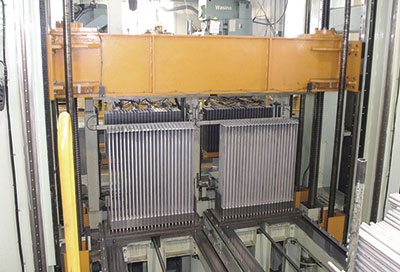
⑥洗浄工程(オイルクリーニング)
成形完了後にプレス機にて使用した油分を炭化水素系溶液によりバブリング洗浄を行い、加工中に付着したオイルを取り除きます。
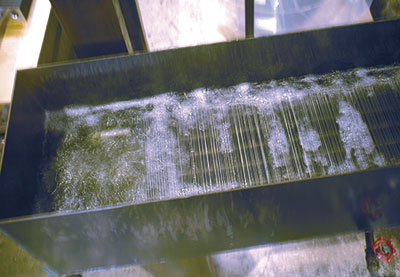
⑦溶接機
各フィンチューブを連結するU字型のベンドやヘッダーカバーを溶接します。素材によりアーク溶接、アルゴン溶接を使い分けます。容易な部分はロボット溶接を行い、ベンド部など高度な技術を要する部分は、2年以上の溶接経験があり、社内の特殊溶接認定試験に合格したエキスパートが担当します。
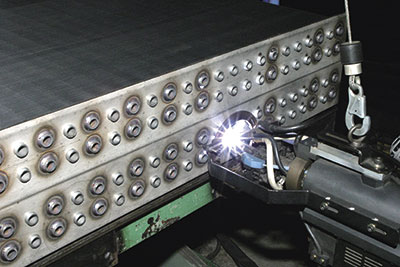
⑧気密試験
溶接が完了したエレメントのチューブ内に所定の空気圧を加え、水槽内に沈めます。気泡の洩れがないかを確認します。
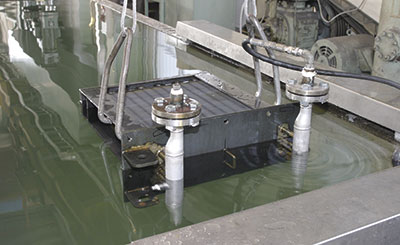
⑨酸洗処理・塗装・仕上げ
溶接による「焼き」の部分に酸の溶剤を塗り、洗浄します。使用後の溶剤は地下のピットに溜め、中和装置で中和させた後に排水します。また、外装は「耐熱シルバー」、つまり銀粉塗装です。使用中のヒーターは高温になるため、特に耐熱性の高い塗料を選定しています。
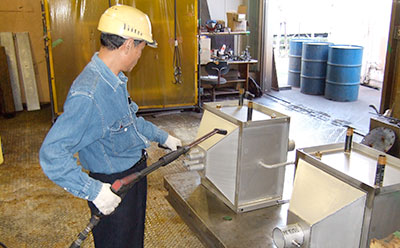
⑩組み立て
各熱交換器のケーシング取り付け~組み込み、連結。
⑪蒸気燃焼(スチームヴィング)
耐圧部の社内検査合格後、チューブ内部にボイラーからの蒸気を入れ、機器全体を加熱することにより、加工ライン中に付着した油脂分を加熱蒸発させ、脱脂処理を行います。客先使用時の白煙の発生を抑える様つとめております。
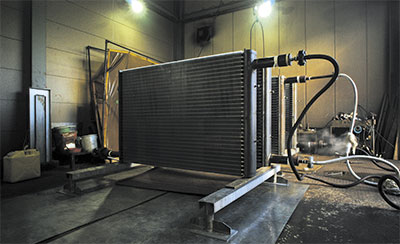
⑫走行クレーン
重量物を搬送するため吊上能力10tの走行型天井クレーンをはじめ、計4台のクレーンが工場内の各ラインを結んでいます。
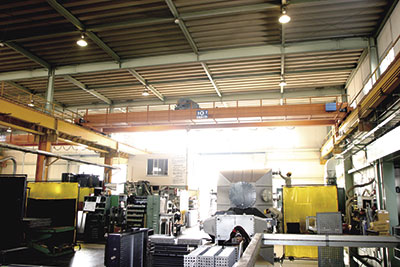
検査・検品体制
私たちの製造プロセスは、機工、溶接、組立エリアに大別できます。品質管理を徹底させるため、各エリアにおいて厳重な検査を実施しています。
【機工】各部寸法検査/開先加工検査
【溶接】各部寸法検査/PT検査/RT検査/
水没洩れ検査/気密耐圧検査
【組立】外形寸法検査/塗装完成検査
機械設備
・全自動プレートフィン圧入機:2台
・大型レーザー加工機:1台
・エアーコンプレッサー:台
・水圧テストポンプ:1台
・テスト用水槽(10.5×2.5×4.8m):1台
・旋盤(4m):1台
・NCドリリングマシン:2台
・ベンディングマシン:2台
・ブレーキプレス:1台
・横向自動シール溶接機:2台
・アーク溶接機:13台
・アルゴン溶接機:13台
・炭酸ガス半自動溶接機:7台
・コマツ高速シャー:1台
・コマツ油圧シャー:1台
・パワープレス:4台
・ジブクレーン(1t):5台
・走行クレーン(10t):1台
・走行クレーン(4.8t):1台
・走行クレーン(2.8t):1台
・走行クレーン(2.5t):1台
・全自動帯鋸盤:2台
・平板開先加工機:2台